How Does an Amazon FBA Warehouse Work and What are the Conditions? I Worked at One
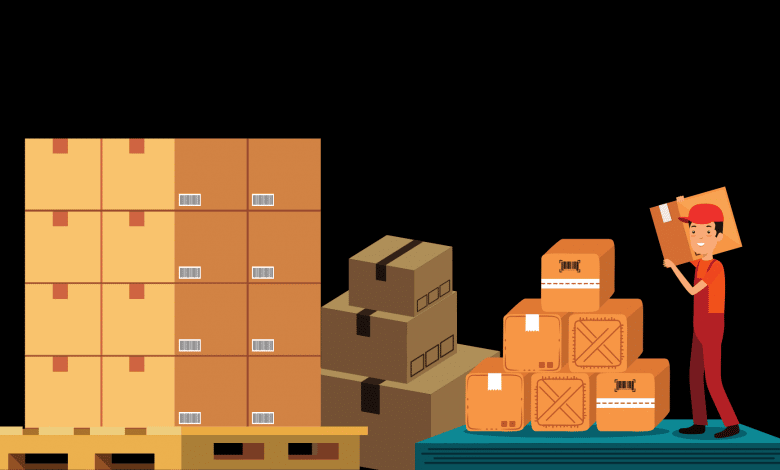
For years I've been trying to get a tour of an Amazon warehouse. These are actually possible at a few Amazon warehouses, but the waitlists are huge and I've never been able to successfully get a tour.
So while eating ramen one night and reading a local newspaper, I saw an ad that Amazon was hiring for their Vancouver warehouse and knew this was the perfect opportunity to finally get my tour! Best of all, by working for Amazon for a few days I would get a truer narrative of how an Amazon FBA warehouse actually works than I ever could from a tour.
Here's a detailed report of my time working for Amazon for a week.
Related Listening: Episode 161 – What I Learned Working at an FBA Warehouse
The Hiring Process
I just sold my business at the end of 2016 so I have a lot of free time. So I applied just before Christmas for a job in their warehouse (surprise surprise – Amazon hires A LOT of people from Black Friday to Christmas).
The “interview” took place in a portable parked inside the parking lot of the FBA warehouse. When I say interview, I use this term in the loosest sense – me and a bunch of other people (the interviewees were disproportionately made up with a lot of Syrian refugees who had just arrived in Vancouver) basically filled in a sheet with our contact information, gave some ID and were told: “welcome to Amazon”.
For some odd reason, they hired me after the Christmas rush in January, which was probably a good thing as working during the holidays means working a mandatory 60-hour workweek. Amazon has basically five positions:
- There are stockers who receive inventory off the trucks and put it in trucks
- There are pickers who find the products that need to be shipped
- There are packers who box up the products and label them
- There are shippers who load everything onto trucks
- There are problem solvers who resolve things like missing stock and damaged items
I got chosen to be a picker for their YVR3 warehouse in Vancouver. It's their largest warehouse in all of North America in terms of cubic footage.
A Side Note – Limited Photography
I wish I could have taken more pictures of the inside of the warehouse, but Amazon has a very strict no cellphone/no pictures policy and entering and leaving the warehouse is akin to going through airport security in Israel.
Upon entering the building you must go through a locked turnstile that requires your employment badge. When you actually enter the warehouse you're forbidden from bringing your cell phone (officially because they would not be able to verify if it was your phone or merchandise but unofficially for productivity reasons).
Upon leaving you must go through a metal detector, which invariably goes off because of the steel-toed shoes you're required to wear, and thereafter you're randomly selected for a full-body search.
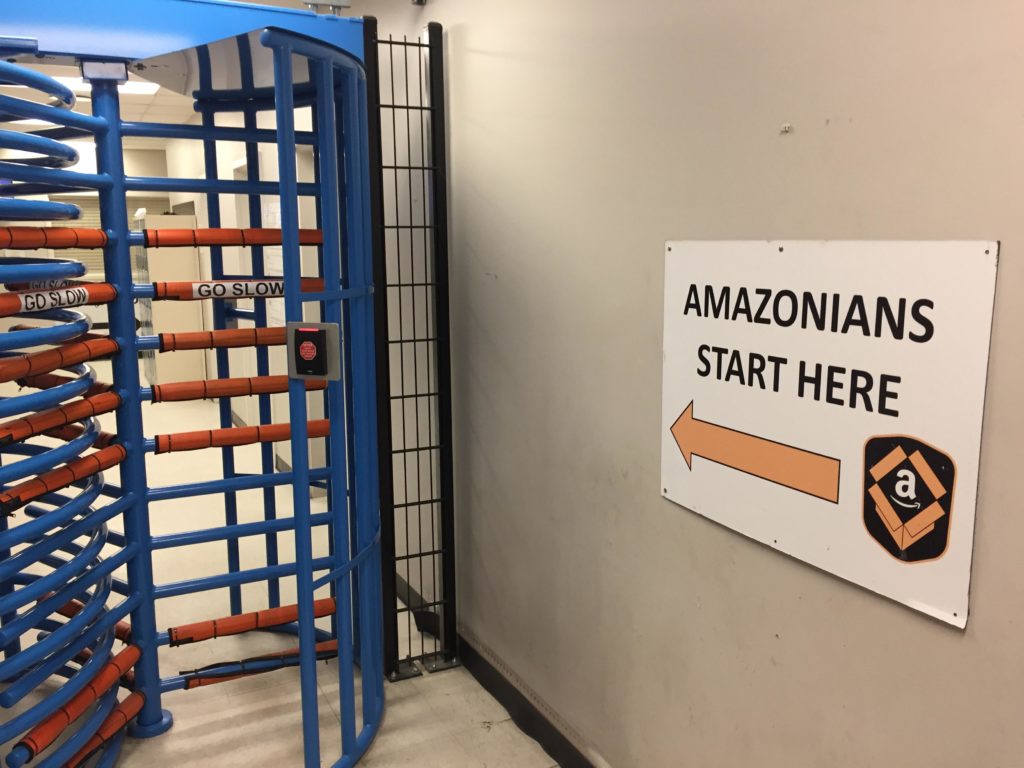
My Observations
I only worked there for a week (I planned on making it two weeks but ran into some childcare issues) but it was more than enough time to get a good feel for things. Here's some of my observations over my few days working for Amazon.
What a Work Day Looked Like and the Overall Working Environment
The first day consisted mostly of safety and corporate culture training. The most surprising thing from all of the training though was the lack of indoctrination of overall Amazon culture into warehouse staff.
I fully expected for at least one of the videos to include a welcome message from Jeff Bezos. Instead, we got a poorly edited welcome message from one of the ex-vice presidents. I'll bet the tech support in Bangalore even gets a welcome message from Jeff! It sort of felt like warehouse employees were treated as second-class citizens within Amazon.
With that being said, the overall morale at the warehouse seemed pretty positive.
After the initial training day, we were basically thrown to the wolves and worked a regular day of work. Every day began with a short 5-minute group stretch. After that, everyone picked up a bar code scanning gun and went to work.
The bar code scanner was everyone's lifeline. You would get all of your tasks for the day through this scanner, i.e. “Today you'll be picking multiple item orders in section C of the warehouse” and the bar code scanner would give you a list of all the items you were required to pick. It was such a fool-proof process that my 1.5-year-old daughter could probably be as effective as me if she could walk just a little bit faster.
Once you had your scanner, you would take a cart (a glorified shopping cart basically), and walk around the warehouse picking items as your scanner guided you until your cart was full. Once your cart was full, you would drop it off at a parking area for all of the full carts.
The packers would then take these carts and pack everything. One of the most baffling things was how there was a complete lack of carts. I would wait around 5 or 10 minutes sometimes to get a cart and many others would do the same thing. And on top of this, many of the carts were in horrible shape with missing or broken wheels. Really Amazon? What would it take to have an excess of carts in excellent shape?
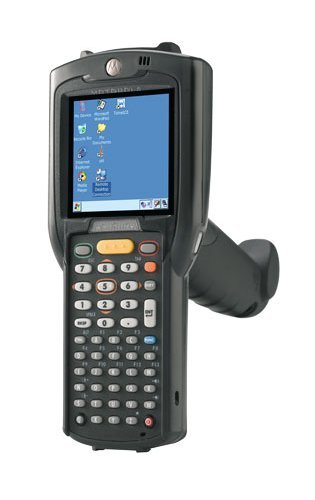
Throughout the day we would actually “run out of work”, in other words, there would be no more items to pick. The warehouse was clearly overstaffed. But showing just how much order volume gets pushed through Amazon, all you would have to do is wait a few minutes and wait for people to order some more stuff on Amazon and you would get assigned another 50 or so items to pick.
Overall, the morale of the warehouse was quite good, at least given the fact, that everyone was working pretty gruelling 10-hour days.
I expected to be working with a bunch of societal delinquents who hated their lives. I was prepared to be on guard about being attacked by a disgruntled employee with a box cutter at any time. Surprisingly though, the job seemed to attract a lot of younger, very normal and social people – either those funding their backpacking trips abroad or university students taking a semester off.
The overall positive morale of the warehouse probably had a lot to do with the pay. Amazon seems to have a bit of a recruitment issue and subsequently, they tend to overpay. They start you off at $13.75 and there's a lot of opportunity for mandatory overtime and voluntary overtime. One can easily earn $40,000+ working at their warehouse. It's a tough job, but you get paid well and you work with good people.
Their Warehouses Are Big and Constantly Expanding
This probably doesn't come as a surprise but Amazon warehouses are big. The warehouse I was working at didn't have any of the capacity issues that many of the warehouses in the U.S. seem to be having because a) Amazon FBA isn't quite as popular in Canada yet, b) Amazon is planning for growth and basically had just doubled this warehouse's size.
Speaking with one of the area managers, he told me that they try to get every truck unloaded and received into inventory within 24 hours. When I asked about any backlog he was visibly puzzled as they clearly didn't have such issues at this warehouse. I've actually shipped products to this very warehouse and the products were always received into stock in a timely manner.
The warehouse I worked at consisted of several zones. Some of the zones were organized logically. For example, zone B had all of the small items (despite this being an oversize warehouse, they still had thousands of small items such as DVDs and USB sticks) on bookshelves like you would find in a library. Zone C was pallet racking stacked about 3 stories high that you needed a PIT truck to get access to (I never got to drive one of these, unfortunately). However, many other zones were basically just pallets stored away with seemingly no logic, as I'll get to later.
As a testament to the size of the warehouse, on the second day my supervisor came up to me and asked why the system showed me as inactive for 55 minutes (the crux of pretty much every position at Amazon rests upon a bar code scanner that tracks everything, including your activity). Despite what my supervisor may have thought, I wasn't snoozing somewhere, I was simply walking from one end of the warehouse to the other and trying to find the aisle!
Multiple FCs in a Region Take Specific Items
The warehouse I was working at was the region's “Oversize” warehouse. If you've made an FBA order for 1 Oven and 1 Oven mitt and had it go to two different warehouses in the same state, this is why. Ditto if your order requires special prep – not every warehouse is set to handle specific types of items.
With that being said, Amazon has a constant stream of trucks ferrying items back and forth between their warehouses. So for example, if a customer made an order on Amazon for that same Oven and Oven mit, Amazon would put the oven mitt on a truck and send it to the oversize warehouse so the two items could ship together and save on shipping costs.
Amazon Sells a LOT of Diapers and TVs
It felt like 25% of the entire warehouse was occupied with TVs and boxes of diapers. This might be an exaggeration but they warehoused and sold a LOT of both of these items. On a side note, it made me appreciate how much waste is caused by baby diapers.
How to See How Much Your Competitors Are Importing from China
Want to see how much your competitors are importing from China?
Custom import records are public information in the United States and there are multiple tools that allow you to simply search for a company name and see exactly how much these companies are importing from China.
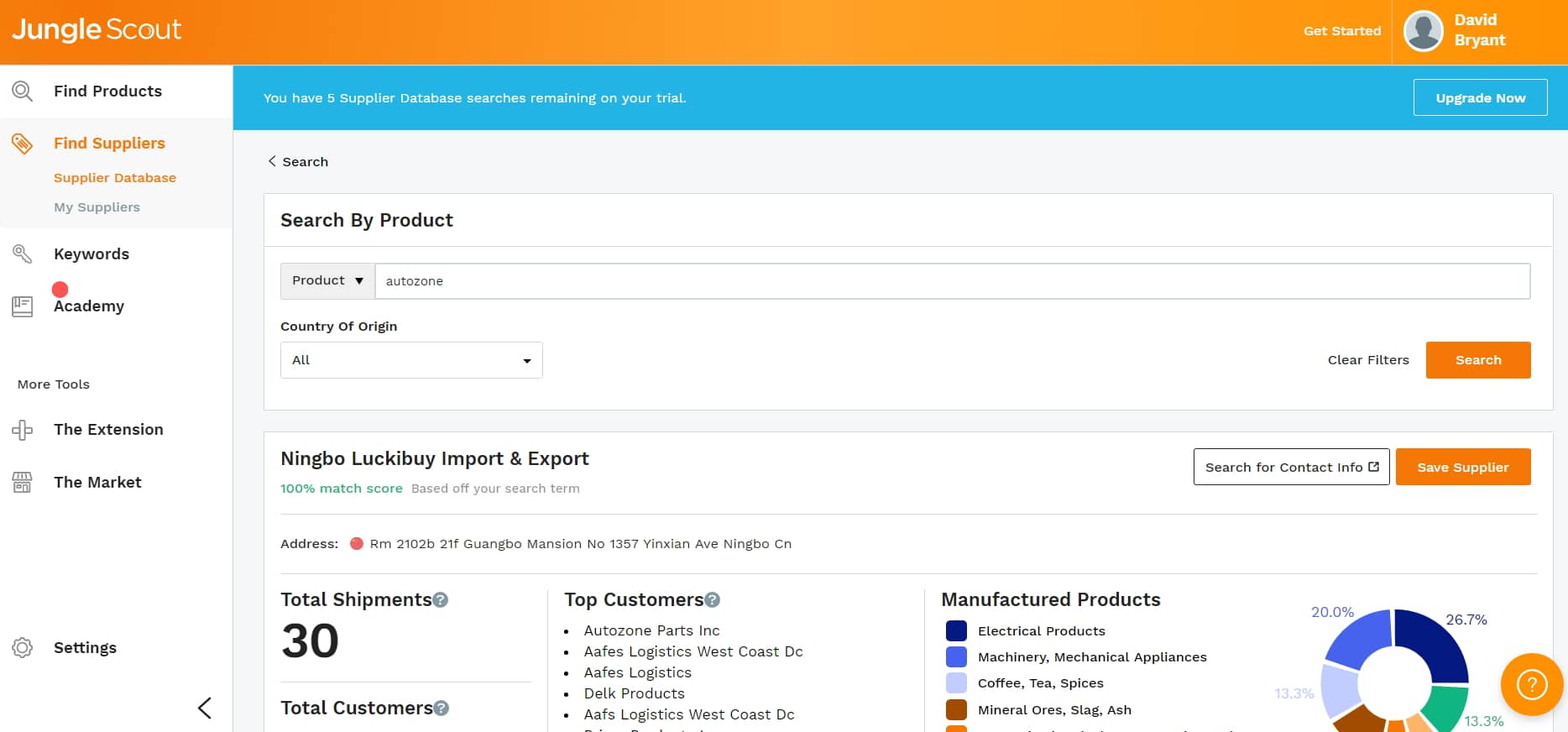
My favorite tool for this is Jungle Scout's Supplier Database tool which costs less than $50 a month (other more expensive options include Import Genius and Panjiva). These tools will neatly summarize all of the information included on a particular company's Bill of Lading information such as product type, quantity, and supplier name/address.
Amazon Warehouses Are Still Primitive
One of the things I was most excited about working at an Amazon warehouse was commanding the army of robots and drones picking and packing items.
Wrong.
There was not a single robot (let alone drone!). All of the picking and packing were done absolutely manually. I felt like I was working on a prison chain gang breaking boulders.
What Amazon does have in place is an EXCELLENT tracking system. Every picker and packer has a bar code gun which is their absolute lifeline. It tracks how many items you pick in an hour, where in the warehouse you've travelled to, what types of items, etc.
You have certain metrics you have to adhere to called your “rate”, i.e. you'll be expected to pick 40 items in an hour. If you miss your rate significantly, you get talked to and coached. If you consistently miss your rate you won't have your contract renewed.
They evaluate you completely on objective and fair performance metric. The result was a) the culture seemed to be extremely good and b) no one gives a crap how you do your job as long as you do it (so much in fact that one of my coworkers every day would disappear for 25 minutes and nap on a dog bed in some far-flung corner of the warehouse).
There Isn't Some Massive Conspiracy to Lose/Damage Your Items
Anyone who uses Amazon FBA knows how much stuff they lose and or damage, so much so that I've heard conspiracy theories float around that Amazon purposely loses and damages items just so they can resell them and lower the effective price of your items.
Again, wrong.
The fact is, Amazon loses a lot of stuff. If a picker accidentally places an item in an adjacent bin, it will go missing for quite a while. Also, given how rapidly their warehouses are expanding (especially YVR3 that I was working at) many people don't even know where certain sections of the warehouse are, let alone where a single item in that warehouse is. Eventually, the item will turn up but you'll likely have been reimbursed by then.
That was the other striking thing about losses, how little rhyme or reason there seemed to be to organization. They would have a $2000 laptop stacked randomly in the same gaylord with an oven and bowling ball (and of course pickers were less than gentle sorting through a Gaylord while trying to meet their rate).
It's not my picture below, but it's exactly how the YVR warehouse looked like with hundreds and thousands of gaylords stacked with completely unrelated items.
As for damage, Amazon has a very liberal ‘damage' policy. On a TV or electronic, if there's a hole on a box larger than a coin, the picker must mark it as damaged. On everything else, if there's a hole larger than a playing card, the picker must mark it as damaged.
Once an item is marked as damaged, the item goes to a single person in the warehouse who will decide the extent of the damage and at which point either Amazon resells it or sell it to a third party.
Why Amazon Fees are So Expensive During Peak Times
There's a single word that strikes fear into every Amazon warehouse employee – peak
Peak is referred to as the time between Black Friday and Christmas. During peak, every employee has mandatory 60-hour work weeks (6 days a week for 10 hours a day).
In Canada at least, this means Amazon has to pay 1.5x pay for 20 hours of overtime per week. Given that Amazon already has to overpay ($13.75 starting) to recruit enough staff, this means they're paying $20+ an hour in many cases for a relatively unskilled and uneducated worker. And their turnover is huge.
So if you ever wonder why your rates go up so much around the holidays, this is a big part of the reason why.
Be Careful with Multipack Items
If you happen to sell a multipack of a particular item, be veryyyy clear with your labeling on your packaging. There's nothing more confusing than when a picker gets an order for “4 xCharmin Toilet Paper”. Does that mean 4 case packs? 4 packages of 4 toilet papers? Or one package of 4 toilet papers? And there's a bit of a flaw in the way Amazon scans in multipacks that allows mistakes regarding multipacks to happen very frequently.
The solution: make use of liberal notes to pickers and packers on your packaging. For example “DO NOT OPEN” stickers, “CASE PACK”, “TEAM LIFT”, “FRAGILE: GLASS INSIDE”, etc. They really help the entire logistics process.
Also, you can clearly mark the contents of the package and/or what constitutes damage (to avoid a picker from liberally marking an item as damaged that isn't actually damaged).
We used to sell an item that was practically indestructible but the boxes would frequently get damaged as the boxes would be damaged and the picker would think the item inside was damaged. In hindsight, a simple sticker on the item saying something along the lines of “Boat anchor inside, slight box damage is acceptable” would have avoided a lot of products from being marked as damaged.
Conclusion
If there's one thing I learned while working at Amazon, it's to be forever grateful to the people both shipping items for our businesses and for our personal purchases. These people work hard!
This is especially true during the holidays when they're working 60-plus hours! After this, I learned that Amazon isn't ruling the ecommerce world through some black magic and alien technology, they're doing it through air-tight standard operating procedures.
Hopefully, this article gives some insight into the inner workings of an Amazon warehouse for FBA Sellers out there. I'm happy to answer any questions I can given my limited experience there. I am sure this article will also find the eyes of potential employees at Amazon warehouses and I'll be happy to answer any questions for you as well – just post in the comments section below.
..another great article..thanks David. Always wondered what it is like in an Amazon Warehouse.
Great article and very interesting to read. It actually explains a lot about some of the issues we are having which make us scratch our head and go WTF where they thinking… How could they loose a whole pallet of my stuff? This makes sense… Question: what did you think about Canadian FBA – since it is growing along with size and number of warehouses and sending products to Canada only, would it then mean that a) they are expanding their Canadian operations = they are confident and have long term plans to support these warehouses and b) More space is required for growing number of product demand = sales are growing in Canada. We had tried Canada in the past, but bailed, because sales were dismal at the time. This sounds like it is time to give it a try again… What do you think?
IMO, they are ambitious about their Canadian sales. While I worked there they definitely had excess capacity and staffing, so I don’t think they’re there quite yet but I’m sure soon.
Amazon is a big a part of lorge mnc comonay that to big full fillment center in india and states and distcs etc my 2019 to 2022 my best role of Inbond associate but present I want to direct amazon in any job role with only full fillment center role
Thank you amazon
Hi David, I have read your article. IAs a small businessman, if I have to find suppliers from overseas like India, Indonesia or China and rest other parts of countries.Is their any directory of suppliers listed.
Thanks for the report.
You’re welcome Jason.
I need my cellphone is there a way I can give it to them or put it in a locker for after work. I need my phone and I dont drive. I have no were to leave it. What should I do ?
Yes, there are lockers. You can’t use it in the warehouse though.
Do you have to go through security to get to the lockers?
Can’t remember. I dont think so though as far as I can remember. Lockers then security.
Great article!
Thanks.
Very interesting article, lots of useful information!
How about seasonal workers….. Do any become full time blue badge employees?
Depends on how many hours they worked I believe.
Very much thanks, just started at Amazon on Boundry Rd in Ottawa, Brand spanking new Warehouse a million sg ft.
It is a job for sure, I’m 58 and it requires alot of attention and protein bars, lol
I figure with 3 years in that Warehouse I’ll be promoted several times
Good luck Steve! It’s a good way to stay in shape :)
My huge question is: Does Amazon warehouses typically have a locker area for employees? What are employees supposed to do with their cell phones who don’t have cars to leave them in?
Yes.
Is it true that employees pee in The bottle ?
You’re in Canada. They get away with more in the US, you know, ‘Merica, “Greatest Country in the nation”! (yes, it’s been said and written) Tracking has become tighter since 2016, there’s no assurance of becoming an actual Amazon hire and you know our “medical care”.
Thank ou for best support amazon